3D Machining (Billet Pistons)
The advantage of having pistons made using 3D machining is that the customer can try various configurations before we make any forging tooling. This means that when the final design is achieved, we can make a "no compromise" forging tool. If a forging tool is made first, and then design and development continues, the customer may end up with a less than ideal forging with regards to thickness and weight, which then requires further tooling to be made, again at extra cost.
Though costly at first, 3D prototyping is the best policy in the long term, especially for "cutting edge" development of leading race engines where in the initial stages many changes are usually needed. Due to the lack of optimum grain structure of a piston produced this way, along with various other factors, fatigue life is somewhat reduced.
It is therefore recommended that they are only used for development work and not in very high stress racing applications such as Formula 1, GP Motorcycle racing etc. Having said that, we can make one off sets of pistons, this way if we feel that the stresses imposed are not going to be detrimental to the life of the component. This makes an ideal solution for small quantity batches of pistons for lower performance applications where we do not have a suitable forging available. |
|
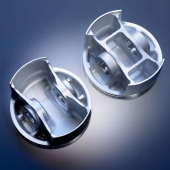 |