About Accralite Pistons
Accralite Pistons is a company specialising in the design and manufacture of small and medium batch quantities of forged pistons used in high performance engines all around the world. Originally founded in 1990, the company became part of Omega Pistons Ltd in 2009.
Accralite is now part of Omega Pistons
As from the 5th December 2009 Accralite Pistons became a part of Omega Pistons Ltd. This brings together the two leading privately owned British forged piston manufacturers.
Omega Pistons Ltd and Accralite Pistons can now design and produce a piston and all of its components in one building.
Accralite Pistons new phone number will be 0121 559 6778, fax 0121 559 6779 and will continue making pistons from their new address at Oak Barn Road, Halesowen, West Midlands. B62 9DW.
- When you receive a forged piston, is it made from extruded 2618A bar to Aerospace specifications and purchased from one of the leading mills in Europe, that exceeds all required racing specifications by far, all with traceability right back to its origin?
- Is your piston forged from precision weighted and turned billets, eliminating inferior finishes from stress raisers?
- Is your piston forged using state of the art facilities to aerospace standards with work piece and forging dies at the same temperature helping to eliminate stress as there are no temperature variations throughout the part, giving added grain compression, strength and durability to the finished piston?
- Is your piston forged using a custom designed specific lubricant to give a perfect internal finish adding strength to the piston?
- Is your piston forging heat-treated and artificially aged to allow your piston to meet the highest T6 specification?
- Is it inspected to British Standard Non-destructive Testing Standards that check for imperfections?
- Is your piston forging vapour blasted internally? Not only to relieve stress but also to show any imperfections that could lead to the forging being rejected as not being suitable to our exacting standards.
- Are your pistons designed and manufactured to your exacting needs in-house from one location in the UK?
- Does your piston, when finished and received, have all the relevant machining that could be done to suit its application without the need to specify and pay extra for? You are the customer, not a piston expert, do you know what it needs?
- Is your piston hand finished and individually weighed? Giving it that extra personal touch and grouped into balanced engine sets, with tolerances held so tight it is not unusual to have less than 0.3 grams between a set of pistons.
- Does your piston come with the highest specification rings? Are they made to the world’s highest standards from the highest-grade materials, chosen for the application and manufactured by, what we feel, the worlds leading ring manufacturer who happens to supply all of the F1 racing teams?
- Does your piston come complete with the highest specification clips? They are sometimes over looked as being a crucial component of the piston. They are manufactured from top grade steel to the highest BS standards; with each clip being hand de-burred to help reduce groove wear.
- Do your pistons have longevity, in some cases, lasting over twice as long as that of the competition, saving money and time in costly rebuilds?
Material
RR-58/2618A
Accralite's basic aluminium is called RR-58, or Rolls Royce 58. (2618A) The material was actually developed in the Second World War for the Rolls Royce Merlin engine that powered everything from the Spitfire to Mosquitoes. It was also the engine responsible for turning the American Mustang from an underpowered and over-weight failure, into one of the best bomber-support fighter aircraft of the war. As the story goes the Merlin started to melt pistons when a super-charger was fitted to boost the power, so the boffins at Rolls Royce had to develop a new material capable of taking the higher pressures, temperatures and speeds. Not surprisingly the stuff is also used to skin Concorde. RR-58 is exceptionally strong and used to manufacture pistons for nearly all types of motorsport applications.
Design Considerations
Before a piston is designed, Accralite needs to get a list of specifications from the customer. These are known as the terms of reference.’ This is basically an outline of the conditions that the engine designer expects the piston to operate in and include: maximum rpm, maximum torque, bore length, type of fuel, the expected lifespan (in hours) and the ring material specifications. As well as that the designer needs to have combustion chamber shape and size information, and valve intrusion specifications.
From these details the piston manufacturer produces the lightest possible design that’s capable of meeting the customer’s lifespan requirements. It sounds fairly straightforward until you realise how many variables the designer needs to cope with. The shape of a piston in an internal combustion engine, for example, is far more complex than a simple cylinder. The shape needs to take into account gas flow, compression ratios, unequal expansion, valve-intrusion and port timing.
On top of that it needs to be light and it needs to, cope with massive temperatures (380°C) and huge pressures (187 Bar). To put this in perspective, bike tyres are set around 2-3 bar. On top of that pistons are placed under enormous loads; having to travel from up to 35m/s to zero and back to 35m/s as much as 36000 times a minute. Now 35m/s works out at 78mph which doesn’t sound a lot until you realise that it has to slow down and stop, then accelerate back up to speed at a rate of two million one hundred and sixty thousand times an hour. That’s not all. On top of that a piston is required to seal gas, have minimal wear rates, and be reliable.
One of the most interesting things about piston design is that they are not cylindrical in shape at all. In fact when cold they are oval and barrel shaped. The reason for this is because the thickness of the material of the piston varies considerably, and this, coupled with the fact that there’s a temperature gradient running all the way down from the crown to the skirt of a piston (and because the expansion of metal is directly proportional to the temperature), complicates matters so much that they have to be machined in such a way when cold to be perfectly cylindrical when hot. Add to this the basic requirement of minimal weight and maximum strength and suddenly the designer has a fair bit on his plate.
Frequently Asked Questions
Are you an American company?
No, Accralite is a British company, so all our pistons are British manufactured and always have been since we begun in 1990.
Are your pistons forged?
Yes, all Accralite pistons are forged from either 2618A or 4032 extruded bar to aerospace specifications which are produced in one of the leading mills in Europe.
Where are your pistons manufactured?
All Accralites’ pistons are manufactured in-house by our skilled engineers at our fully air-conditioned factory in the heart of England, the epicentre of engineering.
What are the numbers on the underside of your pistons?
There are generally two numbers on the underside of our pistons. The one in the middle of the piston which has been forged in is our forging part number. The number that has been computer engraved onto the piston is our unique piston part number.
Do your pistons come complete with rings, pins & clips?
Yes all our pistons come complete with rings, pins and clips and all prices quoted include these. Using our many years of experience we get to know the perfect ring, pin and clip combination to suit your application, so there is no need for you to get involved with this specialised selection process.
What size do I have to bore to?
Our packaging includes a label that details the nominal bore size that you will need to machine your engine block to.
Can I buy Accralite pistons direct?
In most cases yes you can, but over the years we have created many close relationships with distributors with specialist engine knowledge, enabling them to assist you with technical issues, so please contact us for more information.
Can I become an Accralite distributor?
Yes, we would be more than happy to speak to you about becoming an approved Accralite distributor.
What information do you require to enable you to manufacture a set of custom pistons?
There are many ways to send Accralite an enquiry. Use the telephone, fax, Email or the Web. Information is sent in many different ways. A big budget team, where winning is paramount, will send in a full drawing and ask us to manufacture it along with the tooling!
There are some teams who know their basic dimensions bore, compression height, pin diameter etc., and we then design the piston around these parameters and manufacture the tooling for them.
There are some serious enthusiasts who know their basic dimensions, but do not have a budget for tooling so ask us to manufacture a piston from our existing tooling catalogue.
And then there are the enthusiasts, who can send an existing standard cast piston and ask us to manufacture a forged piston to suit their application, whether that be a higher compression ratio or a turbo conversion and then leave the rest to us.
Today’s piston manufacturer must be constantly in tune with new developments and innovations brought on by the need for faster and more efficient engines. We pride ourselves that we are at the forefront of this technology. Accralite is dedicated to giving our customers the very latest in these developments.
Innovation in design and technological advantages are employed in our search for excellence. We use scientific forensic skills to extract vital information required to keep our development programmes ahead of our competitors. Utilising our Accrasurf series of surface processes we can re-engineer the piston to increase the tribological performance to reduce friction and increase the surface strength.
Research and development are our key issues. Accralite commissions the support of recognised institutes for the development of new materials for design and manufacturing techniques. We can offer our customers a special relationship with the aim to reach perfection in the art of design and manufacturing.
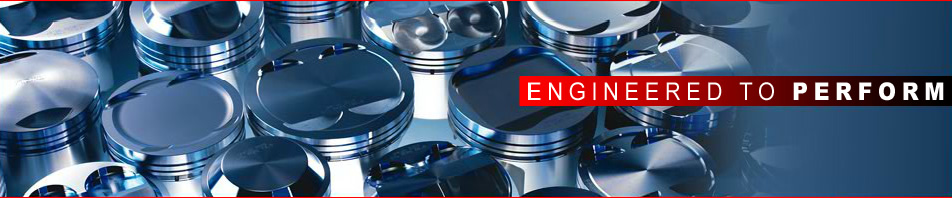
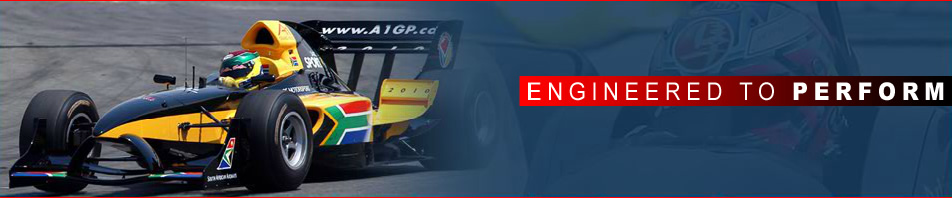
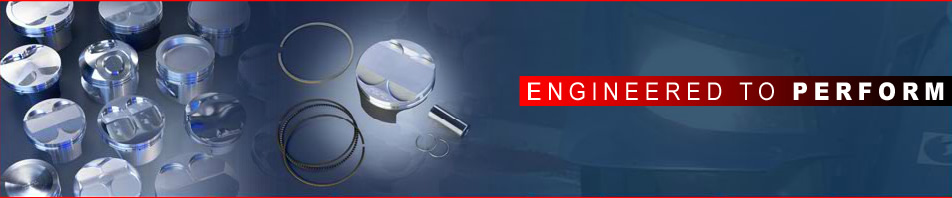
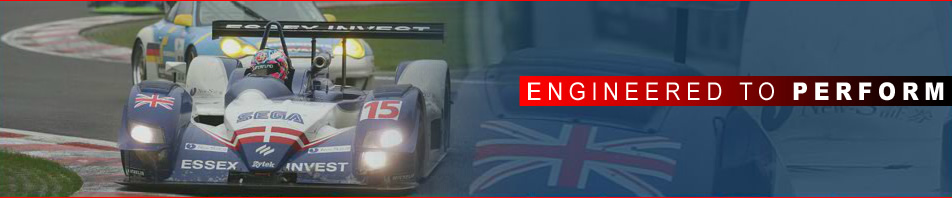
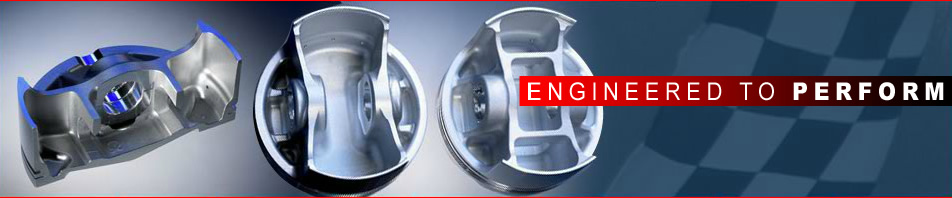
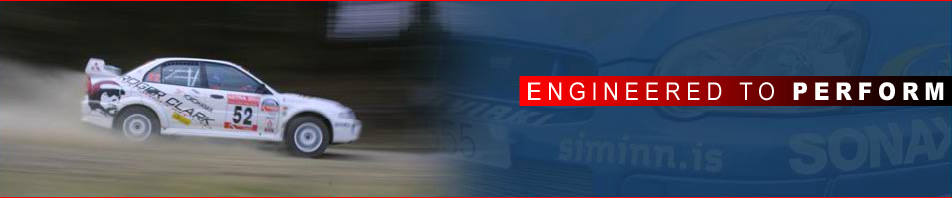